Start
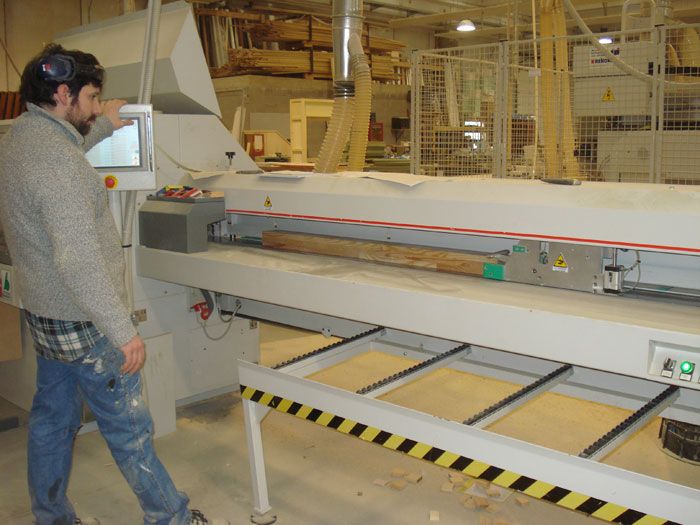
Our technicians can take care of site measurements in order to guarantee a perfect execution of windows and fixture and to make installation easier.
Step 01
After site measurements, we prepare a list detailing all the necessary production materials such as: woods, cuts, hardware, glasses, etc.
Step 02

Every building and room have their peculiar characteristics, that require an accurate material choice. Cutting is carried out by CNC machines and our workers are able to detect the smallest defects in wood, such as knots, cracks, or remains of resin.
Step 03

These processes allow the production of made to measure semi-finished products. Our vanguard machines can make any joint, planing on length and thickness as well as profiling in one step only.
Step 04

A squaring double end tenoning machine allows heading of boards, beams and it is suitable for various cuttings. It is made of three elements, one fixed structure in stainless steel, on which two other structures, one mobile, and one fixed, are mounted. These bear various tools, independently operated, for different processing of wood parts.
Step 05

The better is the execution of single components, the easier is the assembly and glueing of different elements that make up our windows and doors. After the required drying, assembly is executed using special glues that guarantee the shape and dimension of structural elements.
Step 06

Our machinery can cut, drill and groove with high precision to fit hardware, square frames, cut grooves necessary to make perfect alignment of elements.
Step 07

By filling few small gaps that are typical in a natural material such as wood, or that can occur during working phases or handling, we can add to the aesthetics of windows and doors.
Step 08
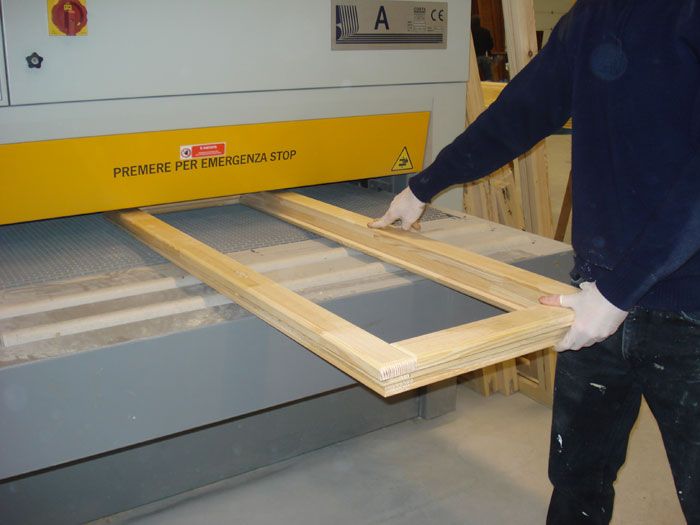
Calibrating machines allow a better surface finishing of panels and wood boards adding accuracy to the product.
Step 09

An innovative thermal cutting for glazing beads and the rubber seal inset make the final setting to arrange all the components.
Step 10

A few procedures need to be done by hand in order to achieve the best results. Manual sanding removes even the smallest defect or any roughness before further finishing steps.
Step 11

The process is done in a flow-coating tub, a system consisting of rain nozzles that spray the product evenly, using less primer than the traditional process by immersion. This process dyes wood and protects it from mould, fungus and insects. Then, windows are stacked into an oven for drying.
Step 12

This finishing can be light or more intense, following customer’s request about wood colour. It can be done even after varnishing to enhance or give an antique finishing to the product.
Step 13

Water coat varnishing is a well known technique that offers many advantages, not only in terms of time saving, but also thank to its resistance to wear and weather conditions, not to mention its lower environmental impact.
Step 14

Surface sanding is the third phase of coating process, before the application of the last coat of varnishing. It is an important step for the protection of doors and windows through time.
Step 15
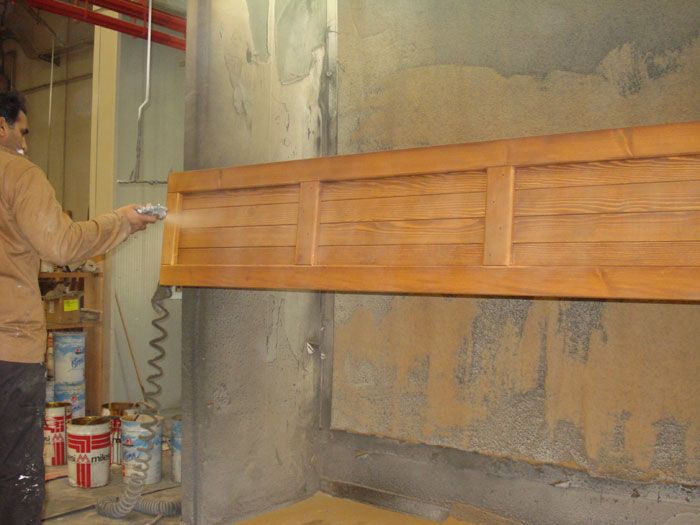
Last coat of varnishing is done in a spray-gun booth. The micro particles of varnish adhere flawlessly to any surface, ensuring that aesthetic finishing that is so valuable for our customers.
Step 16
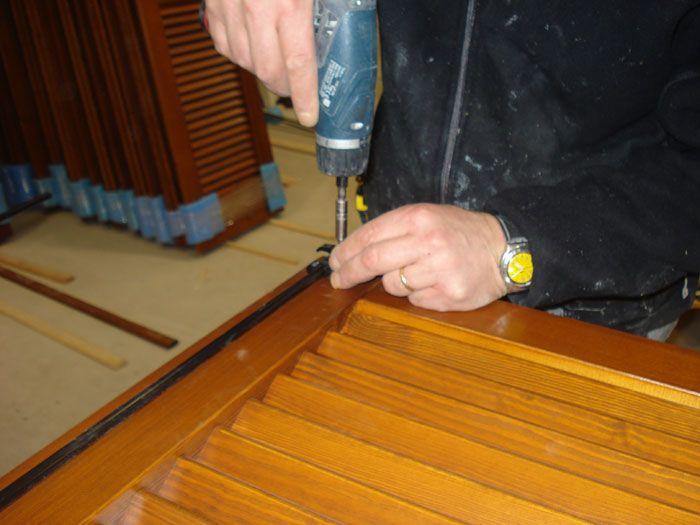
A wide choice of hardware meets customer’s requests matching style and safety against burglar. Our workers take great care in fitting all necessary hardware in the groove cuts executed by CNC machines.
Step 17

In order to avoid demolition and/or masonry works, we have conceived a special frame to preassemble our windows, a system able to guarantee quality and thermo-acoustic insulation.
Step 18

After the final checking, finished products are packed with spongy material and protected with a plastic film, so that to guarantee a safe handling through delivery up to our customer’s house.
Step 19

Transportation is arranged with our means but, if necessary, we can hire third party trucks for on yard delivery. Our products are exclusively installed by our workers to ensure our total quality concept.
Step 20